Table of Contents
In the realm of civil engineering, the acronym “PCC” holds significant importance. PCC full form is Plain Cement Concrete, and it is an essential component in various construction projects. We have covered PCC in detail here.
PCC Full Form in Civil Engineering
PCC stands for Plain Cement Concrete. PCC, is a fundamental building material used in construction.
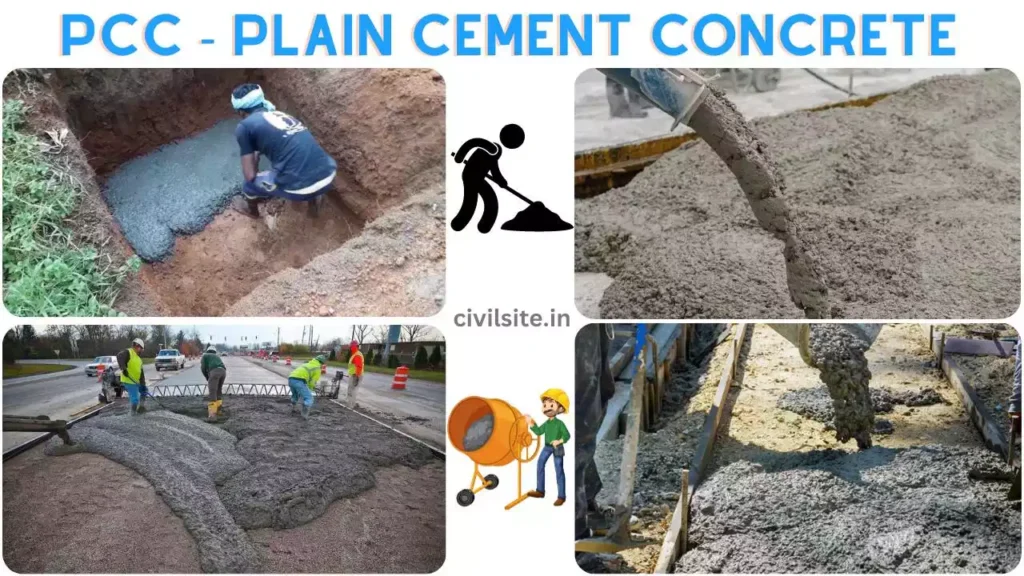
It is primarily composed of three key ingredients:
- Cement: Cement serves as the binding agent in PCC. Portland cement, a widely used variety, is mixed with other materials to form a strong and durable concrete.
- Sand: Sand or fine aggregate should be sharp and angular an should be smaller than mm. San should be free from dust or organic particles.
- Aggregates: Aggregates, including sand and crushed stones, provide structural support to the concrete. They make up the bulk of PCC and determine its strength and density.
- Water: Water is essential to the hydration process of cement, enabling it to harden and gain strength over time.
Preparing PCC
The preparation of Plain Cement Concrete (PCC) involves several steps, from selecting the materials to mixing, placing, and curing the concrete.
Here is a step-by-step guide on how to prepare PCC:
Materials Needed:
- Cement: Portland cement is commonly used in PCC.
- Aggregates: Coarse aggregates (typically crushed stone or gravel) and fine aggregates (usually sand).
- Water: Clean, potable water.
- Formwork: To create the desired shape and dimensions for the concrete.
- Reinforcement (if required): For added strength, especially in structural applications.
- Measuring Tools: To measure the quantities of materials accurately.
- Mixing Equipment: A concrete mixer, if available, or mixing can be done manually with shovels and a mixing platform.
- Compaction Equipment: A vibrating compactor or a manual compaction tool.
- Curing Materials: Such as burlap, curing compound, or wet curing methods.
Steps for Preparing Plain Cement Concrete (PCC):
- Design the Mix: Determine the proportions of cement, aggregates, and water for the desired strength and workability of the concrete. This is known as mix design and should adhere to local building codes and specifications.
- Measurement: Measure the quantities of cement, aggregates, and water according to the mix design. Ensure accurate measurements to maintain the desired mix ratios.
- Mixing: Mix the cement and aggregates (both coarse and fine) thoroughly until they are uniformly distributed. This can be done using a concrete mixer or manually on a clean mixing platform. Gradually add water while continuing to mix until the mix reaches the desired consistency. Avoid using excess water, as it can weaken the concrete.
- Placing: Transfer the mixed concrete into the prepared formwork (the mold that defines the shape and dimensions of the concrete). Ensure that the concrete is evenly distributed and compacted as it is placed to eliminate air voids. If reinforcement is required, place it in the formwork before pouring the concrete.
- Compaction: Use a compactor (either manual or mechanical) to compact the concrete and remove any air pockets. Proper compaction is essential to achieve the desired strength and minimize the risk of cracking.
- Finishing: After compaction, smooth the surface of the PCC using a trowel to create the desired finish. Depending on the application, you can choose from various finishing options, such as a broom finish, trowel finish, or a more decorative finish for aesthetic purposes.
- Curing: Curing is crucial for the proper hydration and hardening of the concrete. Cover the freshly poured PCC with wet burlap, plastic sheeting, or apply a curing compound to retain moisture and maintain a suitable temperature for a specified curing period, typically at least seven days.
- Protection: Protect the freshly placed concrete from external factors like rain, direct sunlight, and extreme temperature fluctuations during the curing period.
- Testing: Perform quality control tests on the cured concrete to ensure it meets the desired strength and durability requirements.
- Finishing Touches: Once the concrete has cured, remove the formwork and clean the surface to achieve the desired appearance and functionality.
Properly preparing PCC involves careful attention to the mix design, material selection, and construction practices to ensure the concrete meets the project’s requirements for strength, durability, and appearance.
Recommended For You:
- Difference between Plinth beam and tie beam
- Types Of Beams In Construction
- 40+ Different Types of Wood
- Checklist for Beam and Column Shuttering
- Complete Reinforcement Details For Column, Beams And Slab
Application of PCC
Plain Cement Concrete (PCC) is used in various construction applications where a sturdy and level surface is required.
Its primary purpose is to provide a strong base or foundation for further construction activities. Here are some common applications of PCC:
- Foundation Beds: PCC is commonly used as a foundation bed or base for buildings and structures. It helps to distribute the load of the structure evenly onto the soil beneath.
- Flooring: PCC is used as a flooring material in residential, commercial, and industrial buildings. It can be left as a plain, smooth finish or polished for a more decorative appearance.
- Roads and Pavements: PCC is used for the construction of rigid pavements and road surfaces. It provides a durable and load-bearing surface for vehicles and pedestrians.
- Sidewalks and Walkways: PCC is an ideal material for constructing sidewalks, walkways, and pedestrian pathways due to its durability and smooth surface.
- Driveways: Many residential driveways are constructed using PCC due to its strength and longevity.
- Parking Lots: PCC is used for constructing parking lots, especially in areas with heavy traffic.
- Airport Runways: PCC is commonly used for the construction of airport runways and taxiways because of its ability to withstand heavy aircraft loads.
- Retaining Walls: PCC is used as a base for retaining walls to provide stability and prevent erosion.
- Pipe Bedding: PCC can be used as bedding material for pipes, ensuring proper support and alignment.
- Stormwater Drainage: PCC is used in the construction of stormwater drainage systems, providing a stable and durable channel for water flow.
- Culverts: PCC is used to construct culverts, allowing the passage of water under roads and railways.
- Bridges: PCC is used in bridge abutments, piers, and other structural components to provide a stable foundation.
- Utility Trenches: When utility lines such as water, gas, or electrical lines are laid underground, PCC is used to backfill and provide support around the pipes or conduits.
- Tennis Courts: PCC can be used as a base for tennis courts, providing a stable and even playing surface.
- Basketball Courts: Similar to tennis courts, PCC is used for basketball court construction.
- Septic Tanks: PCC is used in the construction of septic tanks and their associated components.
- Ramps and Loading Docks: In industrial settings, PCC is used to construct ramps and loading docks to support heavy machinery and loads.
- Sump Pits: PCC is used to create the base for sump pits and pumps in basements and crawl spaces to manage groundwater.
- Machine Foundations: PCC is used to create stable foundations for heavy machinery and equipment in factories and industrial facilities.
- Swimming Pool Bases: PCC is used as a base for swimming pools to provide a stable foundation.
These are just some of the many applications of Plain Cement Concrete in the construction industry.
Its versatility and durability make it a valuable material for a wide range of projects, from residential buildings to infrastructure and industrial facilities.
PCC v/s RCC
Characteristic | PCC (Plain Cement Concrete) | RCC (Reinforced Cement Concrete) |
---|---|---|
Composition | Cement, sand, coarse aggregates, and water | Cement, sand, coarse aggregates, water, and reinforcement (usually steel bars or mesh) |
Tensile Strength | Lower tensile strength | Higher tensile strength due to reinforcement |
Structural Use | Typically used for non-structural applications such as leveling beds, bedding for footings, pavements, sidewalks, and floorings. | Used for structural elements like beams, columns, slabs, foundations, and other load-bearing members. |
Strength | Provides basic compressive strength for support and stability. | Offers both compressive and tensile strength, making it suitable for carrying structural loads. |
Reinforcement | No reinforcement materials used. | Reinforcement materials (steel bars or mesh) are added to enhance tensile strength and structural integrity. |
Applications | – Foundations – Bedding for footings – Pavements and sidewalks – Floorings – Roads and driveways – Non-structural elements | – Building frames – Slabs (e.g., flooring, roof, and bridge slabs) – Beams and columns – Retaining walls – Bridges – Other load-bearing structures |
Properties of PCC
PCC exhibits several essential properties that make it a preferred choice in construction. It is used in various construction applications, primarily for providing a stable and level base for structures. Here are some key properties of PCC:
- Strength: The strength of PCC primarily depends on the ratio of cement to aggregates and the curing process. It is not as strong as reinforced concrete but provides adequate strength for non-structural applications.
- Durability: Properly mixed and cured PCC can be highly durable, especially when it is used for flatwork like pavements or floors. Adequate curing helps prevent cracking and enhances durability.
- Workability: PCC should have a good workability to facilitate its placement and compaction. The mix should be easy to transport and shape into the desired forms.
- Density: PCC has a relatively high density due to the use of aggregates. This density contributes to its stability and load-bearing capacity.
- Shrinkage: PCC can shrink as it cures, which can lead to cracking if not controlled. To minimize shrinkage cracking, control joints or expansion joints may be used, and proper curing techniques should be employed.
- Abrasion Resistance: Depending on the quality of aggregates used, PCC can offer good resistance to abrasion, which is important for pavements and floors subjected to heavy traffic.
- Water-Cement Ratio: The water-cement ratio is a critical factor in PCC mix design. An excessive amount of water can weaken the concrete, while too little water can make it difficult to work with. A proper balance is crucial to achieve the desired strength and durability.
- Curing: Proper curing is essential to achieve the desired strength and durability of PCC. Curing involves maintaining adequate moisture and temperature levels for a specified period to allow the concrete to hydrate and gain strength gradually.
- Setting Time: PCC has a setting time, which is the time it takes for the concrete to harden after mixing with water. This setting time can be adjusted by using different types of cement or additives.
- Cost-Effectiveness: PCC is generally more cost-effective than reinforced concrete because it uses fewer materials and is easier to work with. It is commonly used for foundations, pavements, and non-structural applications.
- Weather Resistance: PCC can withstand various weather conditions, but it may deteriorate over time when exposed to harsh environmental factors like freeze-thaw cycles and chemical exposure. Proper maintenance can extend its lifespan.
- Appearance: PCC surfaces can be finished in different ways to achieve the desired appearance. For example, it can be left with a rough or smooth finish, stamped, stained, or polished for decorative purposes.
PCC is a versatile construction material with various properties that can be adjusted through mix design and construction practices to meet specific project requirements.
Properly designed and executed PCC can provide a reliable and cost-effective solution for a wide range of construction applications.
Advantages of PCC
- Cost-Effective: PCC is generally more cost-effective than reinforced concrete due to its simpler composition and construction process.
- Strength: While not as strong as reinforced concrete, PCC provides adequate compressive strength for many non-structural applications like pavements, floors, and foundations.
- Durability: When properly mixed, placed, and cured, PCC can be highly durable and resistant to wear and tear, making it suitable for long-lasting applications.
- Versatility: PCC can be used for a wide range of applications, including roads, sidewalks, building foundations, and as a base for other construction elements.
- Ease of Construction: It is relatively straightforward to prepare and place PCC, making it a popular choice for various construction projects.
- Availability: Cement, aggregates, and water, the primary components of PCC, are readily available in most regions, making it easy to source materials for construction.
- Fire Resistance: PCC has inherent fire-resistant properties, which can be advantageous in some construction scenarios.
- Sound Insulation: PCC can provide some level of sound insulation, which is useful in floors and walls to reduce noise transmission.
Disadvantages of PCC
- Low Tensile Strength: PCC has low tensile strength, which makes it susceptible to cracking under tensile loads. This weakness can be addressed by using reinforcements or other materials for specific applications.
- Brittle: PCC is relatively brittle, meaning it can fracture suddenly without warning when it reaches its tensile strength limit.
- Cracking: PCC can experience shrinkage cracking if not properly cured or if the mix design is not well-balanced. Control joints or expansion joints may be necessary to manage cracking.
- Limited Structural Use: PCC is not suitable for structural elements subjected to heavy tensile loads unless reinforced with materials like steel.
- Weight: PCC is heavy, and excessive thickness can add significant weight to structures, which may not be suitable for all applications.
- Maintenance: Over time, PCC surfaces may require maintenance and repairs due to wear, abrasion, or cracking.
- Environmental Impact: The production of cement, a key component of PCC, generates carbon dioxide emissions. Efforts to reduce the environmental impact of PCC may involve using alternative cements or incorporating recycled materials.
- Limited Aesthetic Options: PCC has a relatively plain appearance and may not offer the same aesthetic possibilities as other decorative concrete finishes.
Do’s and Dont’s of PCC Work
Making Plain Cement Concrete (PCC) requires adherence to certain do’s and don’ts to ensure the quality and durability of the concrete. Here are some important guidelines to follow:
Do’s:
- Do Plan Properly: Plan the PCC work meticulously, including mix design, materials procurement, and scheduling, to avoid delays and ensure a successful project.
- Do Ensure Proper Mix Design: Design the concrete mix according to the project’s requirements and specifications, considering factors like strength, workability, and durability.
- Do Use Quality Materials: Use high-quality cement, aggregates, and water to achieve the desired strength and durability. Follow local standards and codes for material selection.
- Do Properly Cure the Concrete: Curing is essential for PCC. Keep the concrete moist and at the right temperature for the specified curing period to promote proper hydration and strength development.
- Do Control Water-Cement Ratio: Maintain the correct water-cement ratio to avoid excessive water content, which can weaken the concrete. Follow the mix design closely to achieve the desired consistency.
- Do Proper Compaction: Ensure thorough compaction of the concrete using appropriate tools (manual or mechanical) to remove air voids and improve the concrete’s strength.
- Do Use Reinforcement When Necessary: If structural requirements demand it, use appropriate reinforcement, such as rebar or mesh, to enhance the concrete’s tensile strength.
- Do Follow Safety Practices: Prioritize safety by using personal protective equipment (PPE) and following safety guidelines and procedures on the construction site.
- Do Check for Proper Formwork: Ensure that the formwork is set up correctly, is stable, and can withstand the pressure of the concrete without bulging or deforming.
- Do Monitor Weather Conditions: Be aware of weather conditions, especially when pouring concrete outdoors. Extreme heat or cold can affect curing and workability.
- Do Properly Finish the Surface: Depending on the intended use, finish the concrete surface as required. For instance, use a broom finish for slip resistance on pavements.
Don’ts:
- Don’t Rush the Process: Avoid hurrying through any stage of the PCC work, as haste can lead to mistakes and compromised quality.
- Don’t Use Excessive Water: Resist the temptation to add excess water to the mix to make it easier to work with. This can weaken the concrete and reduce its durability.
- Don’t Over-Vibrate: Excessive vibration during compaction can cause segregation of aggregates and lead to uneven concrete. Follow the recommended vibration guidelines.
- Don’t Neglect Curing: Neglecting proper curing can result in weak and cracked concrete. Don’t skip or rush the curing process.
- Don’t Pour Concrete in Rainy or Extremely Hot Weather: Avoid pouring concrete during heavy rainfall, as it can wash away the cement paste. In extremely hot conditions, take measures to prevent rapid drying.
- Don’t Neglect Formwork Inspection: Regularly inspect the formwork to ensure it remains intact and properly supported throughout the pouring process.
- Don’t Overload Fresh Concrete: Avoid walking or placing heavy loads on freshly poured concrete before it has had a chance to cure properly.
- Don’t Skip Surface Finishing: Neglecting surface finishing can result in a rough or uneven surface that may not meet project requirements.
- Don’t Disregard Safety: Safety should be a top priority. Don’t compromise on safety measures, and ensure that all workers are aware of and follow safety protocols.
- Don’t Ignore Quality Control: Continuously monitor the quality of the concrete mix, placement, and curing to ensure that it meets project specifications.
PCC Full Form in Civil Engineering
The full form of PCC is “Plain Cement Concrete.” PCC refers to a construction material or structural element made by mixing cement, fine aggregates (such as sand), and water in a specific ratio.
It is typically used as a sub-base or base layer in various construction applications, such as road construction, foundation beds, and floor slabs. PCC provides a stable and level surface for the subsequent layers of construction and helps in distributing loads evenly.
Thus PCC full form in civil engineering is Plain Cement Concrete.
Frequently Asked Questions on PCC
What does PCC stand for in civil engineering?
PCC stands for “Plain Cement Concrete.” It is a vital construction material used in civil engineering projects.
What are the main ingredients of PCC?
The primary ingredients of PCC include cement, aggregates (such as sand and crushed stones), and water.
What is the purpose of PCC in construction?
PCC serves as a foundational layer in construction. It provides a sturdy base for structures like buildings, pavements, and roads.
What is the recommended ratio for mixing PCC?
The most common mix ratios for PCC are 1:2:4 (cement: sand: aggregates) for general use and 1:1.5:3 for higher-strength applications.
How is PCC prepared?
PCC is prepared by carefully measuring and mixing the ingredients (cement, aggregates, and water), placing the mixture in formwork, and then curing it to ensure strength and durability.
What are the key properties of PCC?
PCC possesses properties such as excellent compressive strength, durability, workability, and cost-effectiveness, making it suitable for various construction applications.
How is PCC different from RCC (Reinforced Cement Concrete)?
PCC is plain concrete without any reinforcement, while RCC includes steel reinforcement bars to enhance its tensile strength.
Can PCC be used for residential construction?
Yes, PCC is commonly used in residential construction for foundations, floor slabs, and other structural elements.
What precautions should be taken during PCC curing?
During curing, it’s essential to keep the PCC surface moist by sprinkling water regularly and protecting it from direct sunlight, extreme heat, or rapid drying.
Is PCC environmentally friendly?
PCC is considered environmentally friendly because it doesn’t release harmful chemicals into the environment. It can also be recycled.
Can PCC be used for decorative purposes?
While PCC is primarily used for structural purposes, it can be polished and finished to achieve a decorative look for surfaces like countertops and floors.
What is the lifespan of PCC structures?
Properly designed and maintained PCC structures can have a lifespan of several decades, depending on the quality of materials and construction practices.
Can PCC be repaired if it cracks or deteriorates over time?
Yes, PCC can be repaired by filling cracks and addressing surface damage. Regular maintenance can extend its lifespan.
Can PCC be used for underwater construction?
Yes, PCC can be used for underwater construction with the addition of specialized admixtures that ensure proper curing and bonding even in submerged conditions.
What are some common issues that can occur with PCC?
Common issues with PCC include cracking, scaling, and surface imperfections. These can often be mitigated through proper design, construction practices, and maintenance.
Can PCC be recycled or reused?
PCC can be recycled by crushing and using it as a base material for new construction projects. Recycling helps reduce waste and conserves resources.
Conclusion
In conclusion, Plain Cement Concrete (PCC) is a fundamental component in civil engineering and construction. Its ingredients, preparation methods, and properties make it a versatile and reliable material for various applications. Understanding the intricacies of PCC is crucial for ensuring the success and durability of construction projects.
1 thought on “PCC Full Form In Civil Construction | PCC Preparation, Ingredients Properties”