Table of Contents
Rebar is a steel reinforcement used in concrete structures to provide added strength and support. Rebar is a short form for Reinforcing Bar.
It is typically embedded within the concrete to counteract tension forces and enhance the overall load-bearing capacity of the structure.
Types of Rebar
Rebar, short for reinforcing bar, comes in various types, each designed to cater to specific construction needs. The choice of rebar type depends on factors such as project requirements, environmental conditions, and budget considerations.
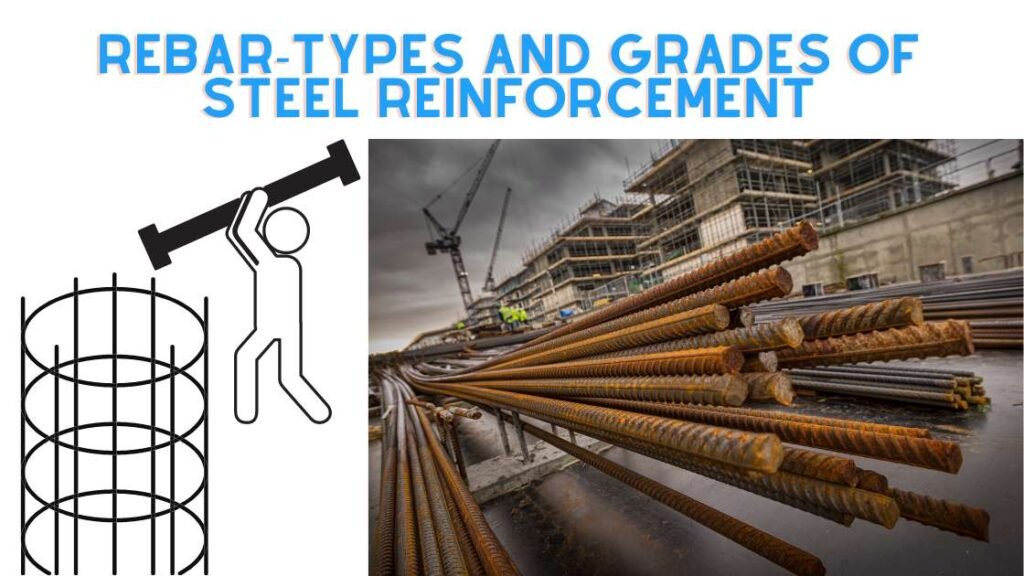
Here are the primary types of rebar commonly used in construction:
1. Mild Steel Rebar
Mild steel rebar, also known as black rebar, is the most commonly used type due to its cost-effectiveness and versatility.
It’s made from carbon steel with low carbon content, making it suitable for various applications. Mild steel rebar is often used in simple structures where high strength isn’t a primary concern.
2. Carbon Steel Rebar
Carbon steel rebar is a step up from mild steel rebar in terms of strength. It contains higher levels of carbon, which lends it greater tensile strength.
This type of rebar is utilized in projects that require increased load-bearing capacity, such as bridges, high-rise buildings, and infrastructure subjected to heavy loads.
3. Epoxy-Coated Rebar
Epoxy-coated rebar is regular steel rebar coated with a layer of epoxy resin. This coating provides excellent corrosion resistance, making it suitable for structures exposed to harsh environments, such as those near the coast or in areas with high humidity.
The epoxy coating acts as a protective barrier that prevents moisture and corrosive agents from reaching the underlying steel.
4. Stainless Steel Rebar
Stainless steel rebar is known for its exceptional corrosion resistance properties. It’s an excellent choice for projects located in corrosive environments, such as chemical plants or coastal structures.
Stainless steel rebar maintains its strength and appearance over time, even in the face of exposure to chemicals, saltwater, and other corrosive elements.
5. Galvanized Rebar
Galvanized rebar is coated with a layer of zinc to provide corrosion protection. This type of rebar is commonly used in projects where the concrete will be exposed to de-icing salts or other corrosive substances.
The zinc coating acts as a sacrificial layer, corroding in place of the steel to prevent damage to the rebar.
6. Glass-Fiber-Reinforced Polymer (GFRP) Rebar
GFRP rebar is a composite rebar made from high-strength glass fibers embedded in a polymer matrix.
It offers excellent corrosion resistance and is particularly useful in applications where electromagnetic neutrality is required, such as in sensitive electronic environments. GFRP rebar is also lightweight and easy to handle.
7. Basalt-Fiber-Reinforced Polymer (BFRP) Rebar
Similar to GFRP rebar, BFRP rebar is a composite rebar made from basalt fibers embedded in a polymer matrix.
Basalt fibers are known for their high tensile strength and resistance to fire and heat. BFRP rebar is often used in projects that require resistance to elevated temperatures or fire exposure.
Grades of Rebar
Rebar, the crucial reinforcement material used in concrete structures, is categorized into various grades based on its yield strength. The yield strength indicates the point at which the rebar will deform and lose its ability to return to its original shape.
Different construction projects demand rebar with specific grades to ensure optimal performance and structural integrity. Here are the common grades of rebar.
Rebar Grade | Yield Strength (psi) | Applications |
---|---|---|
Grade 40 | 40,000 | Versatile choice for light to moderate projects, residential buildings, pavements, small-scale structures |
Grade 60 | 60,000 | Widely used with balanced strength for commercial buildings, bridges, highways, and various structures |
Grade 75 | 75,000 | Suited for heavy-load structures and seismic-prone areas, capable of withstanding substantial forces |
1. Grade 40 Rebar
Yield Strength: 40,000 pounds per square inch (psi)
Grade 40 rebar is a versatile choice suitable for a range of construction applications. With its moderate yield strength, it is commonly used in projects where heavy loads are not a primary concern.
This grade is often selected for light to moderate construction projects, such as residential buildings, pavements, and small-scale structures.
2. Grade 60 Rebar
Yield Strength: 60,000 psi
Grade 60 rebar is one of the most widely used grades due to its balanced combination of strength and affordability. It offers higher tensile strength than Grade 40, making it suitable for a broader range of applications.
This grade is frequently employed in various construction projects, including commercial buildings, bridges, highways, and other structures where durability and load-bearing capacity are crucial.
3. Grade 75 Rebar
Yield Strength: 75,000 psi
Grade 75 rebar is characterized by its higher yield strength, making it well-suited for heavy-load structures and areas prone to seismic activity. Its enhanced strength allows engineers to design structures that can withstand substantial forces.
This grade is commonly used in projects where safety and resilience are of utmost importance, such as earthquake-resistant buildings and critical infrastructure.
Rebar Size Chart
Rebar, or reinforcing bar, comes in various sizes, each denoted by a number. The size of rebar is a crucial factor in determining its weight, strength, and suitability for different construction applications.
The rebar size chart provides valuable information for selecting the appropriate rebar size based on project requirements. Here are some common rebar sizes and their corresponding designations.
Rebar Size | Diameter (inches) | Diameter (mm) | Common Uses |
---|---|---|---|
#3 | 3/8 | 9.5 | Light-duty construction, residential projects |
#4 | 1/2 | 12.7 | Slabs, walls, various applications |
#5 | 5/8 | 15.9 | Foundations, medium-duty projects |
#6 | 3/4 | 19.1 | Columns, beams, heavy-duty structures |
#7 | 7/8 | 22.2 | Larger load-bearing structures |
#8 | 1 | 25.4 | Heavy-duty construction projects |
#9 | 1 1/8 | 28.7 | Significant structural elements |
#10 | 1 1/4 | 31.8 | High-stress areas, large-scale projects |
#11 | 1 3/8 | 34.9 | Heavy-load applications |
#14 | 1 3/4 | 44.4 | Massive construction projects |
- #3 Rebar: Diameter of 3/8 inch (9.5 mm), used for light-duty construction and residential projects.
- #4 Rebar: Diameter of 1/2 inch (12.7 mm), versatile for various applications, including slabs and walls.
- #5 Rebar: Diameter of 5/8 inch (15.9 mm), suitable for medium-duty projects and foundations.
- #6 Rebar: Diameter of 3/4 inch (19.1 mm), commonly used in heavy-duty structures like columns and beams.
- #7 Rebar: Diameter of 7/8 inch (22.2 mm), utilized for larger load-bearing structures.
- #8 Rebar: Diameter of 1 inch (25.4 mm), ideal for heavy-duty construction projects.
- #9 Rebar: Diameter of 1 1/8 inch (28.7 mm), used in significant structural elements.
- #10 Rebar: Diameter of 1 1/4 inches (31.8 mm), suitable for high-stress areas and large-scale projects.
- #11 Rebar: Diameter of 1 3/8 inches (34.9 mm), utilized in heavy-load applications.
- #14 Rebar: Diameter of 1 3/4 inches (44.4 mm), often used in massive construction projects.
The Role of Rebar in Construction
Rebar, short for reinforcing bar, plays a vital role in ensuring the structural integrity and longevity of concrete structures in construction projects. Its primary function is to enhance the concrete’s ability to withstand the various forces and stresses it will encounter over time. Rebar is strategically placed within the concrete to address its inherent weakness in tension and to provide added strength where it’s needed most.
Recommended for you:
- Steel Price Per Kg Today in India 2023
- Density of Cement, Sand, Aggregate and RCC, PCC Concrete
- All Cement Price List Today | Cement Price Per Bag
- Unit Weight Of Steel Bar Weight Per Meter | TMT Bar Weight Chart
- Price List for Building Materials
- Plumbing Work Rate Labour And Material 2023
Counteracting Tension Forces
Concrete is exceptionally strong in compression but weak in tension. When subjected to loads, such as those from the weight of a building or external forces like wind and seismic activity, concrete can crack or even fail under tension. Rebar comes to the rescue by absorbing these tensile forces. It acts as a reinforcement framework that holds the concrete together, preventing the formation of cracks and ensuring the structure’s stability.
Distributing Loads
In addition to counteracting tension forces, rebar assists in distributing loads evenly throughout the concrete. This distribution is essential for preventing localized stress concentrations that could lead to weaknesses or failure points. By reinforcing the concrete, rebar helps ensure that the entire structure can bear the loads it’s designed to support without any specific part being overloaded.
Enhancing Flexural Strength
Flexural strength refers to a material’s ability to resist bending. Rebar significantly enhances the flexural strength of concrete structures. In scenarios where the concrete is subjected to bending moments, such as in beams and columns, rebar helps the structure maintain its shape and integrity. This is particularly important for maintaining the overall stability of the building and ensuring it can handle a variety of loads.
Reinforcing Weak Points
Concrete structures often have areas of inherent vulnerability, such as corners, joints, and areas where openings are created. These weak points can be prone to cracks and deterioration. By strategically placing rebar in these areas, engineers reinforce them, ensuring that these points remain strong and resilient over time.
Ensuring Longevity
The presence of rebar significantly prolongs the lifespan of concrete structures. By preventing cracks, enhancing load distribution, and providing added strength, rebar helps the structure withstand the test of time, minimizing the need for extensive repairs and maintenance.
The Process of Installing Rebar
The installation of rebar, a crucial step in concrete construction, involves a systematic process to ensure proper reinforcement within the concrete structure. The proper placement and arrangement of rebar are essential for the structural integrity and longevity of the final construction project.
1. Design and Planning
Before installing rebar, engineers and construction professionals carefully plan the layout and arrangement of the reinforcement. This includes determining the required rebar sizes, quantities, and configurations based on the structural design and load requirements of the project.
2. Cutting and Bending Rebar
Rebar typically arrives at the construction site in long, straight lengths. Depending on the project’s needs, the rebar may need to be cut to specific lengths and bent to match the design specifications. Special tools and machinery are used to achieve precise cuts and bends.
3. Creating the Reinforcement Grid
The rebar is then laid out in a grid pattern based on the design. This grid is typically created by placing horizontal and vertical rebar bars at specified intervals, forming a mesh-like structure that will provide reinforcement throughout the concrete.
4. Tying Rebar
Once the rebar grid is in place, the bars are securely tied together at the intersections using wire or rebar ties. This process ensures that the rebar remains in its intended position during the concrete pouring phase.
5. Installing Supports
In areas where the rebar needs to be elevated within the concrete, supports such as chairs or spacers are installed to maintain the desired position and ensure that the rebar remains centered within the concrete formwork.
6. Checking Alignment and Positioning
Before proceeding to concrete pouring, the alignment and positioning of the rebar are carefully checked to ensure that it follows the design specifications. Proper alignment is crucial to achieve uniform distribution of reinforcement and prevent potential weak points.
7. Pouring Concrete
Once the rebar is securely in place and aligned, the concrete is poured into the formwork, completely encapsulating the rebar. As the concrete cures and hardens, it fuses with the rebar, creating a strong bond between the two materials.
8. Curing and Setting
After the concrete is poured, it undergoes a curing process to ensure its strength and durability. During this period, the concrete gains its full strength, and the rebar plays a significant role in preventing cracking and enhancing overall stability.
Factors Affecting Rebar Selection
Selecting the appropriate type and size of rebar for a construction project is a crucial decision that significantly impacts the structure’s durability, performance, and overall success. Several key factors influence the choice of rebar, ensuring that it aligns with the project’s requirements and enhances the structure’s structural integrity.
1. Structural Requirements
The load-bearing capacity and overall strength of the structure dictate the type and grade of rebar to be used. Projects with higher loads, such as bridges and high-rise buildings, may require higher-strength rebar to withstand the forces they will encounter.
2. Exposure Conditions
The environmental conditions to which the structure will be exposed play a significant role in rebar selection. Structures in coastal areas or those subjected to corrosive chemicals require corrosion-resistant rebar, such as epoxy-coated or stainless steel rebar, to prevent deterioration over time.
3. Durability Expectations
The anticipated lifespan of the structure also influences rebar selection. Projects intended for long-term use require rebar that can withstand the test of time and resist factors like corrosion, fatigue, and wear.
4. Cost Considerations
Budget constraints often play a role in rebar selection. While higher-strength or corrosion-resistant rebar may offer enhanced performance, they might also come at a higher cost. Balancing performance with budget is essential to ensure cost-effective construction.
5. Project Specifics
Each construction project has unique characteristics that influence rebar selection. Considerations such as the project’s size, complexity, design, and intended use all factor into the decision-making process.
6. Local Building Codes and Regulations
Building codes and regulations set by local authorities dictate the standards and requirements for construction materials, including rebar. Adhering to these codes ensures that the structure meets safety and quality standards.
7. Ease of Installation
The ease of handling and installation of rebar is also a consideration. Some projects may benefit from using lighter or prefabricated rebar materials that simplify the construction process.
8. Environmental Impact
Sustainability and environmental impact are increasingly important considerations. Using eco-friendly or recycled rebar options may align with a project’s commitment to environmental responsibility.
9. Project Timeline
The project timeline can impact rebar selection, as some types of rebar may have longer lead times for production and delivery. Quick-turnaround projects might require readily available rebar options.
10. Engineering Expertise
Consulting with experienced structural engineers and construction professionals is crucial for making informed rebar selection decisions. Their expertise ensures that the chosen rebar meets the project’s requirements and contributes to its overall success.
Advantages of Using Different Types of Rebar
The choice of rebar type can significantly impact the performance, durability, and overall quality of a construction project. Different types of rebar offer unique advantages that cater to specific project requirements and environmental conditions. Here are the advantages of using various types of rebar:
1. Mild Steel Rebar
- Cost-Effective: Mild steel rebar is economical, making it a suitable choice for projects with budget constraints.
- Versatility: It can be used in a wide range of applications, from residential buildings to smaller-scale structures.
- Ease of Handling: Mild steel rebar is easy to cut, bend, and work with during construction.
2. Epoxy-Coated Rebar
- Corrosion Resistance: Epoxy-coated rebar provides excellent protection against corrosion, extending the lifespan of the structure.
- Suitable for Harsh Environments: Ideal for structures in coastal areas or regions with high humidity, where corrosion is a major concern.
- Reduced Maintenance: The protective epoxy coating minimizes the need for frequent maintenance and repairs.
3. Stainless Steel Rebar
- Exceptional Corrosion Resistance: Stainless steel rebar is highly resistant to corrosion, making it suitable for harsh environments, chemical plants, and marine structures.
- Longevity: Structures reinforced with stainless steel rebar can have a longer lifespan due to its resistance to rust and deterioration.
- Aesthetics: Stainless steel’s polished appearance is desirable in architectural applications.
4. GFRP Rebar
- Corrosion-Free: GFRP rebar does not corrode, making it an excellent choice for environments where corrosion poses a significant threat.
- Electromagnetic Neutrality: It does not interfere with electronic or magnetic systems, making it ideal for sensitive environments like hospitals and laboratories.
- Lightweight: GFRP rebar is lighter than steel, making it easier to handle and transport.
5. BFRP Rebar
- High Temperature Resistance: BFRP rebar retains its strength even in high-temperature environments, such as fire-prone areas.
- Corrosion Resistance: Similar to GFRP rebar, BFRP rebar does not corrode, ensuring long-term durability.
- Reduced Thermal Conductivity: BFRP rebar has lower thermal conductivity than steel, making it suitable for projects where temperature fluctuations are a concern.
6. Galvanized Rebar
- Corrosion Protection: The zinc coating on galvanized rebar acts as a sacrificial layer, preventing the underlying steel from corroding.
- Cost-Effective Corrosion Prevention: Galvanized rebar offers corrosion resistance at a lower cost compared to stainless steel.
- Suitable for High-Humidity Environments: Galvanized rebar is used in structures exposed to de-icing salts and humid conditions.
7. Carbon Steel Rebar
- Balanced Strength: Carbon steel rebar offers a good balance between strength and cost-effectiveness, suitable for a wide range of projects.
- Availability: It is readily available and commonly used in various construction applications.
The Importance of Steel Reinforcement
Steel reinforcement, commonly referred to as rebar, is a fundamental component in the construction industry that plays a pivotal role in enhancing the strength, durability, and overall integrity of concrete structures. It serves as a vital element in reinforcing various types of construction, from towering skyscrapers to intricate bridges, ensuring they can withstand the challenges of time, load, and environmental factors. The importance of steel reinforcement lies in its multifaceted contributions to construction projects:
1. Enhancing Structural Strength
Rebar provides concrete structures with the necessary tensile strength that concrete alone lacks. Concrete is excellent at withstanding compressive forces but is susceptible to cracking and failing under tensile stress. By embedding rebar within the concrete, the composite material gains the ability to handle both compressive and tensile loads, creating a structurally robust assembly.
2. Distributing Loads
Steel reinforcement helps distribute external loads evenly across the structure. Without rebar, concentrated loads could cause localized stress points, leading to cracks, deformation, and potentially catastrophic failure. The presence of rebar ensures that loads are dispersed over a larger area, preventing overloading in specific sections.
3. Preventing Cracking
Rebar minimizes the development of cracks in concrete caused by shrinkage, temperature fluctuations, and settling. The tensile strength of rebar counteracts these forces, helping to maintain the structural integrity and appearance of the concrete over time.
4. Increasing Durability
Concrete structures face various environmental challenges, including exposure to moisture, chemicals, and abrasive substances. Rebar, especially corrosion-resistant types, extends the lifespan of structures by preventing premature degradation and minimizing maintenance needs.
5. Adapting to Dynamic Loads
Structures often experience dynamic loads, such as vibrations from traffic, wind, or seismic events. Rebar reinforcement enables structures to absorb and dissipate these forces, reducing the risk of structural failure and enhancing safety.
6. Supporting Architectural Innovation
Architects and designers can push the boundaries of creativity and innovation in construction projects, knowing that rebar reinforcement allows for the realization of intricate designs and unconventional shapes while maintaining structural integrity.
7. Ensuring Safety
The integration of rebar reinforces the safety of occupants and users of structures. Whether it’s a residential building, a bridge, or a commercial complex, the presence of rebar assures stability and reliability, safeguarding lives and assets.
8. Compliance with Building Codes
Building codes and regulations often mandate the use of steel reinforcement in specific types of construction to ensure compliance with safety standards. Adhering to these codes guarantees that structures are built to withstand expected loads and environmental conditions.
9. Extending Service Life
Well-designed and properly reinforced structures have longer service lives. Rebar reinforcement mitigates the effects of aging, wear, and exposure, reducing the frequency of repairs and replacements.
10. Engineering Innovation
The ongoing research and development in rebar technology continue to introduce new materials and techniques, enabling engineers and builders to construct structures that meet evolving performance, safety, and sustainability requirements.
Challenges in Working with Rebar
While rebar plays a crucial role in reinforcing concrete structures, its installation and integration into construction projects can present several challenges. Overcoming these challenges is essential to ensure the proper functioning and longevity of the final structure. Here are some common challenges faced when working with rebar:
1. Handling and Placement
Rebar can be heavy and unwieldy, making its handling and proper placement a challenge. Ensuring that rebar is positioned accurately according to design specifications requires careful coordination and the use of specialized tools and equipment.
2. Complex Designs
For projects with intricate designs or complex reinforcement requirements, properly arranging rebar can be challenging. Maintaining the intended configuration while ensuring proper alignment demands skilled labor and meticulous attention to detail.
3. Corrosion
Corrosion can compromise the integrity of both the rebar and the concrete surrounding it. Selecting the appropriate rebar type and implementing effective corrosion prevention measures are essential to combat this challenge, especially in corrosive environments.
4. Proper Tying
Tying rebar intersections securely is crucial to maintain the intended position during concrete pouring. Inadequate tying can lead to rebar displacement and affect the structural integrity of the concrete.
5. Weather Conditions
Unfavorable weather conditions, such as rain, extreme heat, or cold, can impact the rebar installation process. These conditions may affect the curing of the concrete, potentially leading to cracking or reduced strength.
6. Interference with Other Trades
In multi-trade construction sites, rebar installation must align with other trades’ activities. Coordination among various teams is essential to avoid conflicts and ensure that rebar work proceeds smoothly.
7. Safety Concerns
Handling and placing rebar require adherence to safety protocols. The heavy weight of rebar and the use of equipment present safety risks to workers if not managed properly.
8. Quality Control
Maintaining quality throughout the rebar installation process is essential. Proper inspection, verification of alignment, and adherence to design specifications are necessary to avoid defects and ensure the structure’s performance.
9. Limited Access Areas
In confined spaces or areas with limited access, placing rebar accurately can be challenging. Specialized equipment or alternative installation methods may be required.
10. Changes in Design
Changes to the project’s design during construction can impact rebar installation. Adapting to design modifications without compromising the structural integrity requires flexibility and quick decision-making.
11. Cost and Budget Constraints
Using specialized rebar types or addressing challenges may involve higher costs. Balancing budget constraints with the need for quality and durability is a common challenge.
12. Construction Deadlines
Meeting construction deadlines while ensuring proper rebar installation requires efficient planning, coordination, and skilled labor.
Innovations in Rebar Technology
As construction practices evolve and demand for more sustainable, efficient, and durable structures grows, innovations in rebar technology have emerged to address various challenges and enhance the performance of concrete structures. These advancements aim to improve the installation process, increase structural resilience, and reduce the environmental impact of construction. Here are some notable innovations in rebar technology:
1. Fiber-Reinforced Polymer (FRP) Rebar
FRP rebar, made from high-strength fibers embedded in a polymer matrix, offers a corrosion-free alternative to traditional steel rebar. It is lightweight, easy to handle, and resistant to both corrosion and electromagnetic interference. FRP rebar is especially valuable in environments where corrosion poses a significant threat, such as coastal areas or chemical plants.
2. Shape Memory Alloys (SMAs) Rebar
SMAs are smart materials that can change shape in response to temperature variations. SMA rebar contracts when exposed to heat and expands when cooled. This property allows it to absorb and release stress during temperature fluctuations, enhancing the structural resilience of concrete.
3. High-Strength Steel Rebar
Advancements in metallurgy have led to the development of high-strength steel rebar with yield strengths surpassing traditional rebar grades. This type of rebar allows for more efficient designs with reduced material usage while maintaining structural integrity.
4. 3D-Printed Rebar
Additive manufacturing, or 3D printing, has entered the construction industry, allowing for the fabrication of complex rebar structures with high precision. 3D-printed rebar enables customized reinforcement designs that suit specific project requirements.
5. Self-Healing Concrete with Rebar Sensors
Self-healing concrete incorporates capsules containing healing agents that are released when cracks form. Additionally, embedded sensors within the rebar can detect cracks and trigger the release of healing agents, promoting the autonomous repair of concrete structures.
6. Digital Fabrication of Rebar
Digital technologies and Building Information Modeling (BIM) have enabled the digital fabrication of rebar components. This process involves using automated machinery to shape and assemble rebar according to precise design specifications, streamlining the construction process and reducing waste.
7. Corrosion-Resistant Coatings
Advancements in coatings technology have resulted in innovative corrosion-resistant coatings that can be applied to rebar surfaces. These coatings provide a protective barrier against moisture and corrosive elements, extending the lifespan of the rebar and the concrete structure.
8. Nanotechnology for Rebar Enhancement
Nanotechnology is being explored to improve the properties of rebar materials. Nanoparticles can be incorporated into rebar to enhance its strength, durability, and resistance to environmental factors.
9. Rebar with Embedded Sensors
Rebar with integrated sensors can provide real-time data on strain, stress, and temperature within the concrete structure. This information helps monitor the health of the structure and detect potential issues before they escalate.
10. Recycled and Sustainable Rebar Materials
In line with sustainability goals, research is ongoing to develop rebar materials made from recycled materials, such as reclaimed steel or other eco-friendly composites. These innovations contribute to reducing the environmental impact of construction.
Sustainable Rebar Practices
As the construction industry embraces sustainability and environmental responsibility, adopting sustainable practices related to rebar usage becomes paramount. These practices not only contribute to reducing the environmental impact of construction but also promote the creation of resilient and efficient structures. Here are key sustainable rebar practices:
1. Material Selection
Choosing rebar materials that have a lower environmental footprint is a fundamental sustainable practice. Opting for recycled steel rebar or alternative materials like fiber-reinforced polymers (FRP) reduces the demand for virgin resources and minimizes the carbon footprint associated with production.
2. Life Cycle Assessment (LCA)
Conducting a life cycle assessment of rebar helps evaluate its environmental impact from extraction to disposal. This assessment guides decision-making by identifying opportunities to reduce environmental burdens at every stage of rebar’s life cycle.
3. Corrosion Prevention
Investing in corrosion-resistant rebar options, such as epoxy-coated, stainless steel, or galvanized rebar, enhances the longevity of structures. By preventing corrosion-related deterioration, these choices reduce the need for frequent repairs and replacements.
4. Design Efficiency
Efficiently designing structures with appropriate rebar configurations minimizes material wastage and ensures optimal load distribution. Utilizing advanced software tools, such as Building Information Modeling (BIM), assists in precise rebar placement, reducing excess material usage.
5. Recycling and Reuse
Implementing rebar recycling and reuse programs diverts rebar from landfills and conserves resources. Salvaging rebar from deconstructed structures and incorporating it into new projects reduces the need for new rebar production.
6. Prefabrication
Prefabricating rebar components off-site enhances efficiency and reduces construction waste. Precisely shaped and assembled rebar components can be delivered to the construction site, minimizing on-site cutting and reducing material scrap.
7. Local Sourcing
Sourcing rebar materials locally reduces transportation-related emissions and supports the local economy. It also contributes to the reduction of carbon emissions associated with long-distance transportation.
8. Energy-Efficient Production
Opting for rebar manufacturers with energy-efficient production processes minimizes the environmental impact of rebar manufacturing. Technologies such as electric arc furnaces and energy recovery systems can significantly reduce energy consumption.
9. Low-Impact Coatings
Choosing environmentally friendly coatings for rebar, such as water-based or low-VOC coatings, reduces emissions and eliminates the release of harmful chemicals into the environment during construction and throughout the structure’s life.
10. Education and Training
Promoting awareness and training among construction professionals about sustainable rebar practices is crucial. Proper knowledge and understanding enable the effective implementation of sustainable practices across projects.
11. Certification and Standards
Utilizing eco-certified or eco-labeled rebar products ensures compliance with sustainability standards and certifications, contributing to environmentally responsible construction practices.
12. Collaboration and Innovation
Encouraging collaboration among stakeholders—engineers, architects, contractors, and suppliers—facilitates the adoption of innovative sustainable practices and the sharing of best practices.
Maintenance of Rebar
Proper maintenance of rebar is essential to ensure the long-term integrity, durability, and safety of concrete structures. Regular maintenance practices help prevent corrosion, deterioration, and structural issues, extending the lifespan of the construction. Here are key considerations for the maintenance of rebar:
1. Visual Inspections
Regular visual inspections of rebar and concrete surfaces are crucial. Look for signs of rust, cracks, spalling, or any visible damage that may indicate corrosion or weakening of the structure. Addressing issues promptly prevents them from escalating.
2. Corrosion Prevention
Implement corrosion prevention measures to protect rebar from rust and deterioration. For existing structures, this may involve applying protective coatings, such as epoxy or zinc-based coatings, to rebar surfaces. In new constructions, consider using corrosion-resistant rebar materials.
3. Crack Repair
Address any cracks in the concrete promptly. Cracks can allow moisture and corrosive agents to reach the rebar, accelerating corrosion. Repair cracks using appropriate methods, such as epoxy injection or crack sealants, to prevent further damage.
4. Cathodic Protection
For structures with existing corrosion issues, cathodic protection can be employed. This electrochemical process involves applying a direct current to the rebar, diverting corrosion reactions and extending the rebar’s lifespan.
5. Concrete Cover Inspection
Ensure that the concrete cover over the rebar is intact and meets design specifications. Adequate concrete cover provides a protective layer that shields the rebar from environmental elements and reduces the risk of corrosion.
6. Environmental Monitoring
Monitor environmental conditions that may impact rebar corrosion, such as exposure to saltwater, humidity, or chemical pollutants. Implement measures to mitigate these effects, such as proper drainage systems or barriers.
7. Regular Cleaning
Clean rebar and concrete surfaces to remove dirt, debris, and contaminants that can accelerate corrosion. Regular cleaning helps maintain the rebar’s protective coatings and prevents the accumulation of corrosive agents.
8. Rebar Exposures
Ensure that rebar is not left exposed to the elements for prolonged periods during construction or maintenance work. Exposed rebar is susceptible to rust and damage from environmental factors.
9. Professional Inspection
Engage structural engineers or experts in rebar maintenance for comprehensive assessments. Their expertise can identify potential issues and recommend appropriate maintenance strategies.
10. Documentation and Records
Maintain records of inspections, repairs, and maintenance activities. This documentation helps track the condition of the rebar over time and informs future maintenance decisions.
11. Education and Training
Train maintenance personnel on proper rebar maintenance techniques, including proper cleaning, coating application, and crack repair. Knowledgeable staff contribute to effective maintenance practices.
12. Long-Term Planning
Develop a long-term maintenance plan that outlines regular inspection schedules, maintenance activities, and budget allocations. A proactive approach ensures that maintenance efforts are consistent and effective.
2 thoughts on “What is Rebar? Types and Grades of Steel Reinforcement”