Table of Contents
When it comes to building a sturdy, cost-effective foundation for lightweight structures like garages, sheds, or workshops, floating slabs are a popular choice. Unlike traditional foundations with deep footings, floating slabs “float” on the ground, making them ideal for projects where simplicity and affordability are priorities. However, their design requires careful planning to address challenges like frost heave, moisture, and load distribution.
Floating Slab Construction Design Guide
In this comprehensive guide, we’ll walk you through the step-by-step design and construction process, key considerations, and expert tips to ensure your floating slab stands the test of time.
What is a Floating Slab?
A floating slab is a type of shallow foundation that rests directly on the soil without being anchored to deep footings. It consists of three primary layers:
- Compacted gravel base for drainage and stability.
- Vapor barrier to block moisture.
- Reinforced concrete slab that bears the structure’s load.
Best suited for:
- Detached garages, storage sheds, and workshops.
- Light commercial buildings (e.g., small retail spaces).
- Regions with mild frost conditions or where insulation is added.
Step-by-Step Floating Slab Construction Guide
1. Site Preparation
Goal: Create a stable, level base for the slab.
- Clear the area: Remove vegetation, rocks, and debris.
- Excavate: Dig 12–18 inches below the finished grade to accommodate the gravel base and slab.
- Compact the subgrade: Use a plate compactor to eliminate air pockets and ensure uniform soil density.
- Pro Tip: For weak or clay-heavy soils, add a 2-inch layer of coarse sand before gravel to improve stability.
2. Gravel Base Installation
Purpose: Provides drainage, minimizes frost penetration, and prevents settling.
- Material: Use ¾-inch crushed stone with fines (e.g., ABC gravel) for optimal compaction.
- Thickness: 4–6 inches, compacted in 2-inch layers.
- Slope: Grade the gravel base slightly (1–2% slope) away from the structure to direct water runoff.
3. Vapor Barrier Placement
Why it matters: Prevents moisture from rising into the slab, which can cause mold, cracking, or corrosion of reinforcements.
- Material: 6–10 mil polyethylene sheeting.
- Installation: Lay the barrier over the gravel base, overlapping seams by 12 inches and sealing with tape. Extend it 6 inches up the sides of the excavation to create a moisture-resistant “bowl.”
4. Insulation (For Cold Climates)
Critical in frost-prone areas: Insulation reduces heat loss from the slab and prevents frost heave.
- Material: Rigid foam insulation (XPS or EPS) with an R-value of at least 10.
- Installation:
- Place insulation panels over the vapor barrier.
- Extend insulation vertically around the slab perimeter to create a thermal break.
5. Reinforcement
Prevents cracking: Reinforce the slab to handle shrinkage and light loads.
- Options:
- Welded wire mesh (WWM): 6×6-inch grid (W1.4/W2.9) placed in the upper third of the slab.
- Rebar: #3 or #4 bars spaced 12–18 inches apart in a grid pattern.
- Fiber-reinforced concrete: Adds microfibers to the mix for crack resistance (ideal for light-duty slabs).
- Support: Use plastic or metal chairs to keep reinforcement elevated during the pour.
6. Formwork Setup
Materials: 2×4 or 2×6 lumber, metal forms, or prefab systems.
- Installation:
- Build forms to match the slab’s dimensions and secure them with stakes.
- Check for level and square using a laser level or string lines.
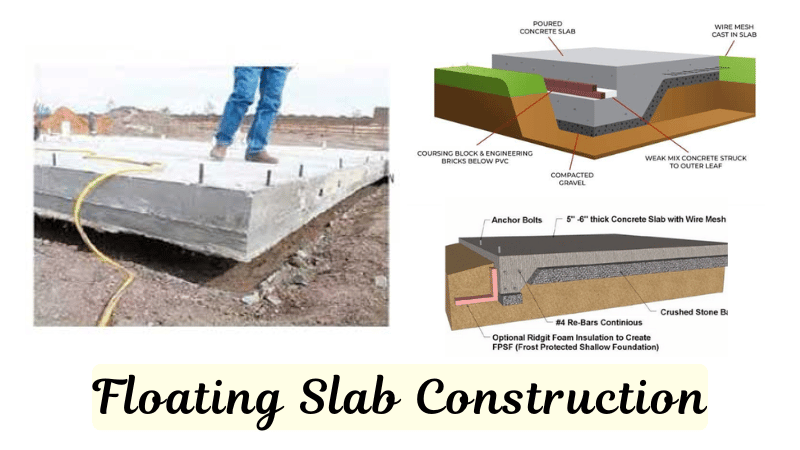
7. Concrete Pouring & Finishing
Key specs:
- Concrete mix: 3,000–4,000 psi strength.
- Slab thickness: 4–6 inches (increase to 6+ inches for heavy loads like vehicles).
- Process:
- Pour concrete evenly into forms, starting from one corner.
- Use a screed board to level the surface.
- Remove air bubbles with a concrete vibrator or by tapping forms.
- Finish with a bull float, then trowel for a smooth surface.
8. Control Joints
Purpose: Control where cracks form due to shrinkage.
- Spacing: Cut joints at 24–36 times the slab thickness (e.g., 8–12 feet for a 4-inch slab).
- Depth: 25% of the slab thickness.
- Timing: Cut joints within 12–24 hours of pouring.
9. Curing
Why it’s critical: Proper curing ensures maximum strength and durability.
- Methods:
- Keep the slab moist with wet burlap or plastic sheeting for 7 days.
- Apply a curing compound for low-maintenance protection.
Design Considerations for Floating Slabs
1. Load Requirements
- Light loads (e.g., storage sheds): 4-inch slab with WWM.
- Heavy loads (e.g., vehicles): 6-inch slab with rebar grid (#4 bars at 12-inch spacing).
2. Frost Protection
- Insulate the perimeter: Use vertical rigid foam around slab edges.
- Increase gravel depth: Up to 12 inches in frost-prone areas to reduce frost penetration.
3. Drainage
- Slope the site: Ensure a 1–2% slope away from the slab.
- French drains: Install if the water table is high or soil drainage is poor.
4. Soil Bearing Capacity
- Ideal soils: Sandy or gravelly soils with good drainage.
- Weak soils: Stabilize with geotextile fabric or lime/cement mixing.
5. Local Building Codes
- Permits: Check requirements for slab depth, insulation, and setbacks.
- Frost line: In cold climates, codes may require frost-protected shallow foundations (FPSF) for floating slabs.
Materials & Tools Checklist
- Materials:
- Crushed stone (ABC gravel).
- Polyethylene vapor barrier.
- Rigid foam insulation (XPS/EPS).
- Welded wire mesh or rebar.
- 3,000–4,000 psi concrete mix.
- Tools:
- Plate compactor.
- Concrete mixer or pump.
- Screed board, bull float, and trowels.
- Joint cutter.
Common Mistakes to Avoid
- Skipping Compaction: Uncompacted soil or gravel leads to settling and cracks.
- Ignoring Vapor Barriers: Moisture intrusion weakens the slab and promotes mold.
- Poor Joint Placement: Inadequate control joints result in random cracking.
- Insufficient Curing: Rapid drying causes weak, brittle concrete.
Floating Slab vs. Other Foundations
Foundation Type | Best For | Cost | Frost Resistance |
---|---|---|---|
Floating Slab | Garages, sheds, workshops | 5–5–8/sq. ft. | Moderate (with insulation) |
Monolithic Slab | Homes, heavy structures | 8–8–12+/sq. ft. | High (footings below frost line) |
Trench Footing | Expansive soils | 10–10–15/sq. ft. | High |
Frequently Asked Questions
Q: Can I build a floating slab on expansive clay soil?
A: Yes, but add geotextile fabric between the soil and gravel, and consider lime stabilization.
Q: How long does a floating slab last?
A: 30–50+ years if designed and constructed properly.
Q: Do floating slabs require footings?
A: No—they rely on the gravel base for load distribution.
Final Tips for Success
- Test soil drainage before excavation.
- Use fiber-mesh concrete in freeze-thaw cycles for added durability.
- Consult an engineer for heavy loads or complex sites.
Conclusion
A floating slab is an efficient, budget-friendly foundation solution for lightweight structures—if you address frost, moisture, and reinforcement needs. By following this guide and tailoring the design to your site’s conditions, you’ll create a durable base that supports your project for decades.